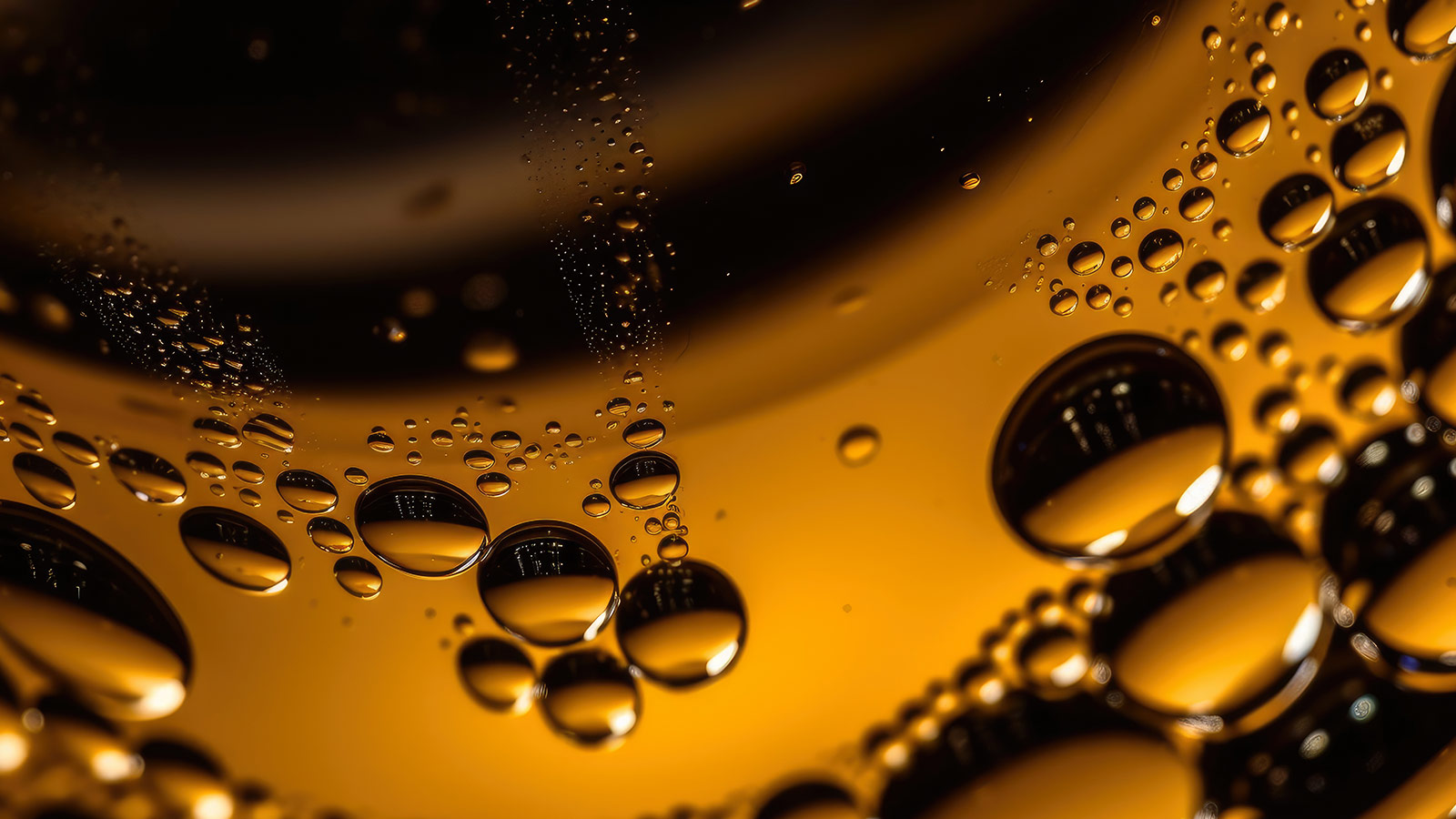
Published May 03, 2024 | 6 minute read
Published May 03, 2024 | 6 minute read
The most important aspects of proper oil storage, transportation, and filtering deal with contamination control, waste reduction, cost savings, and safety enhancement.
Industrial oil can be contaminated by various sources, such as dust, water, metal particles, or bacteria.
It can also become cross-contaminated by different types or grades of oil. This often occurs when the oil containers, pipes, hoses, pumps, or valves are not properly cleaned or labeled, or you transfer oil without proper identification.
Contamination can occur at any point during the storage, transportation, or filtering processes, especially if your industrial oil is exposed to an unclean environment or humid conditions. Improperly sealed oil containers or filters are another common culprit.
Properly managing industrial oil lessens the ingress of contaminants, removes existing contaminants, and extends your oil’s life and performance.
Cross-contamination affects your oil’s quality, which will in turn undermine your equipment’s performance, resulting in damage, malfunction, and failure.
Contaminated oils and their additives exhibit diminished lubricity, altered viscosity, increased acidity and oxidation, and cause sludge formation leading to corrosion, wear, overheating, increased vibration, and leakage.
Oil can spill from containers, pipes, hoses, pumps, and valves during storage, transport, or filtering; this is typically due to human error, equipment failure, or improper installation.
Spilled oil should never be taken lightly. It can cause environmental pollution, soil and water contamination, fires, explosions, and health and safety risks, both to your employees and the communities in which you operate.
Not only is spillage potentially harmful, but it can also be financially costly in the form of wasted oil and expenses to rectify the damages.
Exercising precaution when managing industrial oil protects against degradation, maintains its quality, and curtails the amount to be discarded or recycled.
If you’re looking to cut costs, improving your oil storage, transportation, and filtering processes is a sure way to do it. Improper oil handling increases the costs of consumption, equipment repair, and lost production from unexpected downtime, to say little about environmental compliance.
Industrial oil is degraded by heat, load, and contamination which causes it to lose effectiveness and efficiency. This results in more frequent replacement and disposal.
Alternatively, proper storage, transportation, and filtering optimize usage, improving your equipment’s performance, reducing maintenance needs, enhancing operational efficiency, and lowering your overall costs.
Industrial workers face several safety hazards when operating equipment and handling oil, including fire risk, potential explosions, slipping and falling, and skin and eye irritation, to name a few.
These safety hazards can occur anytime during oil storage, transportation, or filtering. If the oil comes under high pressure or temperature, is spilled or leaked, or isn’t handled with adequate care and protection, you compromise the safety of your employees.
In addition to potential injuries and fatalities, poor oil management can result in revenue losses and fines from regulatory agencies.
As you look to enhance contamination control, improve waste reduction, increase savings, and strengthen safety measures at your facility, there are several best practices you should integrate into your industrial oil management processes:
You’ll encounter several types of oil filtration systems depending on your industrial needs, including vacuum dehydrators for water removal and dedicated filtration systems.
A portable oil filtration machine is a mobile device that filters oil from sundry sources, such as tanks, drums, and reservoirs. It consists of a pump, filter, hose, and nozzle. It removes contaminants, such as dirt, water, metal particles, etc. from your oil and improves quality and performance. It can also transfer oil from one location to another, or dispense it into your equipment.
A wheeled cart that connects to all types of equipment, such as hydraulic systems, gearboxes, large pumps, and turbines. They usually have one or two filters, depending on the level of filtration required—removing impurities (dust, water, and oxidation products), and extending lifespan and efficiency. Filter carts can also be used to flush equipment or change your oil.
A mounted device that cleans oil from large-volume applications, platform style portable oil carts feature multiple filters for removing adulterants (sludge, water, and varnish) from your oil. While maintaining its character and consistency, a platform-style cart can also be employed to transfer oil from one tank to another or to drain.
A vacuum dehydrator is a portable machine that removes the vast majority of free, dissolved, and emulsified water from your oil. It does this by raising the oil temperature while drawing a vacuum. The water then flashes off at a temperature that doesn’t thermally degrade the oil.
You’ll usually find oil and lubrication products from Des-Case, Royal Purple, Bel-Ray, and ATS Electro-Lube are among the most popular for industrial oil management.
A specialist in contamination control products, Des-Case offers filtration, storage, and breather technologies that keep your lubricants clean and dry before they enter your equipment.
ATS Electro-Lube is a leader in automatic lubricating equipment, including single-point, multi-point, and refillable units available in varying sizes and capabilities.
Sunair carries products from both Des-Case and ATS Electro-Lube, supplying industrial technicians and plant managers with the durable and reliable products their equipment needs to continue performing their best. We are passionate about the lubrication products we carry.
Consider also high performance lubricants from Royal Purple and Bel-Ray. These lubricants are pre-filtered and certified clean from the factory, and shipped in virgin poly or steel drums, avoiding the need to filter before storage or use.
Celebrating 50 years in business, Sunair’s team of seasoned professionals is eager to answer any questions you have about oil management and which products are right for your industrial situation.
Receive the latest industry news, once a month. Unsubscribe anytime.
To determine the size of a component mechanical seal, measure the inside diameter of the seal face, the length of the spring, and diameter and thickness of the stationary seat.
Read NowDesigned to handle various hydrocarbons in accordance with the high standards of the American Petroleum Institute, API pumps ranging from end suction to vertical turbine models are commonly used in the petroleum, petrochemical, and natural gas industries.
Read NowRegularly inspecting your mechanical seals and monitoring various factors that could contribute to failure or leakage will help extend their lifespan, while ensuring operational efficiency and safety.
Read NowPairing Sunair Co.’s high-quality equipment with the most impactful automation opportunities within the food manufacturing industry—across the packaging, production, sanitation, product tracing, and quality control phases—enables companies to realize significant operational efficiencies and cost savings.
Read NowSunair Co. carries high-quality propane pumps and compressors from leading manufacturers such as Sundyne, Blackmer, and National Pump to ensure your operations perform safely and effectively.
Read Now2475 Wyandotte Road
Willow Grove, PA 19090
Phone: (215) 657-9800
Fax: (215) 657-9881
Email: sunairco@sunair.com
© Copyright 2025 Sunair Co.
Logos on this page are copyrights of their respective companies. The Sunair logo is a registered trademark of Sunair Co.
Leave a comment