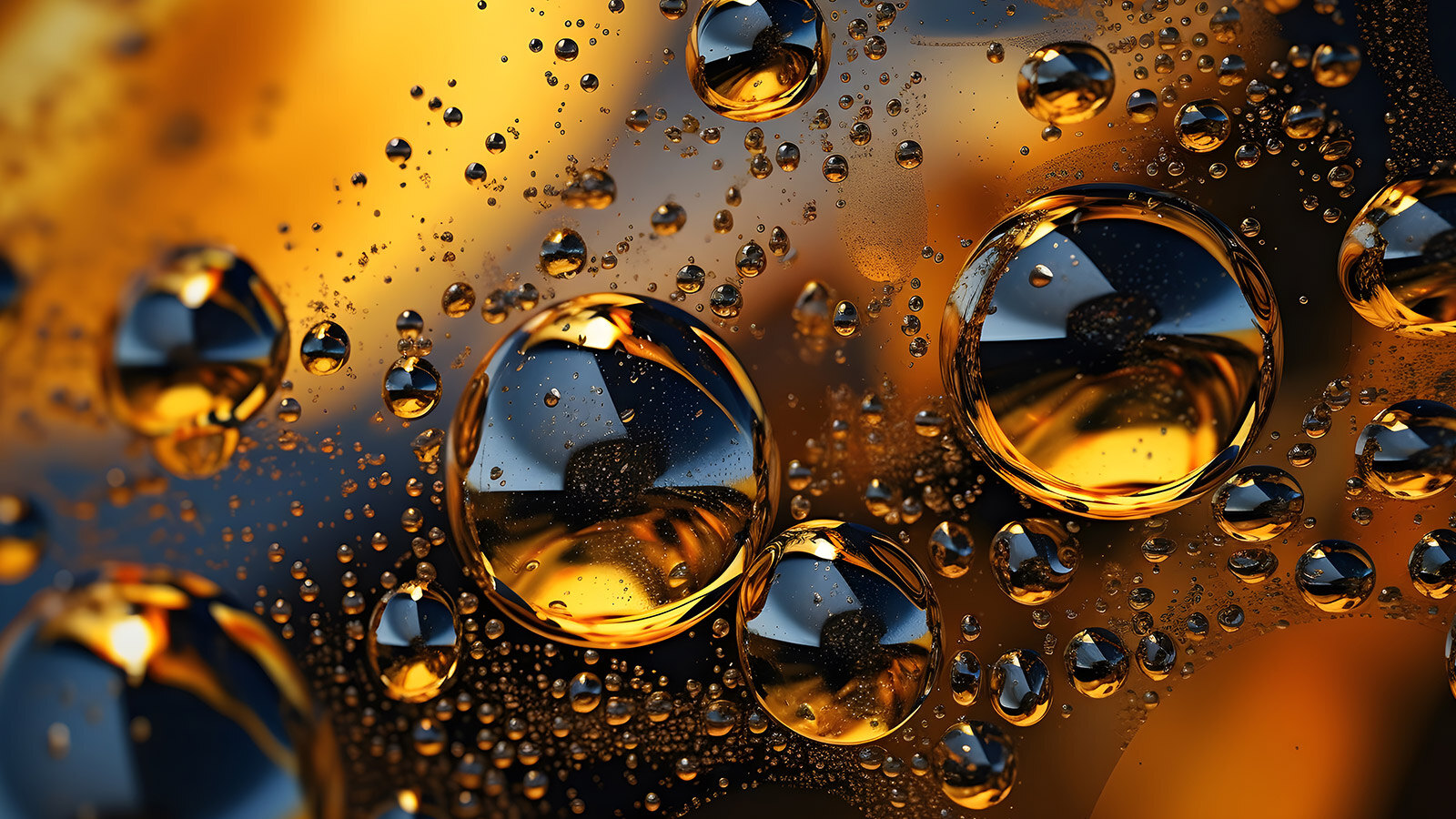
Published May 07, 2024 | 5 minute read
Published May 07, 2024 | 5 minute read
Plant managers, reliability engineers, and technicians know that taking regular machinery oil samples helps to identify potential problems early on and mitigates expensive repairs to your industrial facility’s equipment down the line.
Sampling reveals the conditions of your lubricants and determines asset health. The oil reflects the overall fitness of your industrial machinery.
Several essentials to oil sampling will help you detect problems early, extend oil and equipment life, and reduce downtime and associated costs from unplanned repairs.
Oil sample analysis is a highly effective way to non-invasively gauge the health of your equipment without disassembling it for inspection.
Oil samples are taken from your industrial equipment, tested in a lab, evaluated for signs of wear, contamination, and oxidation, and then analysis is used to inform necessary adjustments or repairs to your machinery.
These tests evaluate viscosity and the presence of harmful particles and contaminants.
Here’s an overview of the basics:
Many industrial plants don’t have the onsite tools necessary to conduct oil analysis, so you’ll likely have to send oil samples to a specialized lab for testing.
To collect an oil specimen, you’ll rely on drop tube sampling, pitot-tube sample valves, pressurized line sampling, or drain port sampling. Drain port sampling is the least desirable and effective method of sampling and should be avoided if possible.
The best oil samples are taken while your machinery is operating. Pitot tubes and pre-installed sample valves make it possible to do so safely and effectively.
Online sampling may not be prudent if doing so puts you at risk of harm or injury. In this case, collecting an oil sample while your equipment is de-energized is fine.
Consult Sunair Co. or your local service provider or chosen lab for instructions on how to gather an oil sample. They’ll be able to share best practices, guidelines, and specifications for their process.
A single oil sample gives you limited information on its own.
You’ll need to conduct routine oil samples to benchmark machinery conditions at regular intervals to judge the condition of oil for continued use. Testing’s greatest value comes from trending successive oil samples and having consistent comparative samples.
Here are several best practices to keep in mind during oil sampling:
Collect an oil sample once your machine has been running for at least 30 minutes. This provides you with an accurate still frame for what’s happening internally. It enables you to capture any contaminants that may be in your lubricant during operation, giving you an accurate picture of what’s going on inside your equipment. Also, before collecting your sample, allow a volume of oil to flow enough to flush the dead space of the sampling equipment to ensure you collect a sample of fresh oil.
Sample consistently from the same location in an active zone within your equipment’s lube system and avoid pulling sediment off the bottom of the sump. Drop tube sampling with a vacuum pump can be used while the equipment is de-energized, but pitot tubes and sample valves can be added that make it possible to intentionally and consistently sample from the same exact location without having to shut down the asset
Retrieve oil samples before they enter filters. As you can imagine, much of the information you’re after, such as contaminants or signs of wear, is distorted when passing through your equipment’s filtration system. To avoid this, collect an oil sample before it enters the filter.
Establish a consistent oil sampling schedule. The lab you partner with should be able to outline how frequently you need to collect oil samples, whether every 1,000 hours, monthly, quarterly, annually, or otherwise. As you gain knowledge of oil life and machinery health through trending, you can adjust your oil sampling schedule accordingly.
Avoid sampling from drain plugs. This will give you an inaccurate sample with an overabundant degree of sediment and other contaminants. Instead, collect from a port, pump, or dip-stick tube. If you must gather from a drain plug, thoroughly clean it out before collecting an oil sample. This will reduce errant testing material.
Maintenance technicians must be consistent. If you have more than one maintenance technician involved in oil sampling, ensure they are trained in precisely the same sampling method.
Multiple technicians collecting oil samples using different methods introduces variance that can undermine the accuracy of your testing. Regularly training technicians and visibly displaying detailed instructions helps reduce opportunities for deviation. Conditions and procedures should be the same every single time.
Deliver oil samples to your lab as soon as possible. This ensures you identify problems with machinery before they become worse. Delays can result in costly repairs.
As you look for oil sampling products that suit your situation, consider Des-Case, which is among the most popular brands for industrial oil sampling and management.
For example, Des-Case manufactures the LT-Series Lubricant Management System (LT-LMS), a straightforward and stackable setup dedicated to top-class filtration, storing, dispensing, and oil sample collection. It’s also customizable, providing you with a broad spectrum of flow rates, container sizes, quick-connect fittings, and steel and HDPE tanks.
Alternatively, Des-Case produces TC Series T Stand filtration products, arguably its most rugged system for industrial oil management. Its heavy-duty system is ideal for large reservoirs with high flow rates and accommodates multiple filter types, including micro-fiberglass drop-in filters, depth filters, and bag filters. This series is designed for decontaminating systems, flushing new or repaired systems, pre-filtering new oil, and collecting oil samples for analysis.
Sunair also partners with Wearcheck for your oil analysis needs.
Sunair carries Des-Case products, among other industry-leading brands for oil sampling and management—supplying your industrial technicians and plant managers with the durable and reliable products your equipment needs to continue performing at its best.
Backed by 50 years of experience delivering reliability-engineered products and services, Sunair’s team of experts is ready to help you identify the oil sampling solution right for your industrial application.
Receive the latest industry news, once a month. Unsubscribe anytime.
To determine the size of a component mechanical seal, measure the inside diameter of the seal face, the length of the spring, and diameter and thickness of the stationary seat.
Read NowDesigned to handle various hydrocarbons in accordance with the high standards of the American Petroleum Institute, API pumps ranging from end suction to vertical turbine models are commonly used in the petroleum, petrochemical, and natural gas industries.
Read NowRegularly inspecting your mechanical seals and monitoring various factors that could contribute to failure or leakage will help extend their lifespan, while ensuring operational efficiency and safety.
Read NowPairing Sunair Co.’s high-quality equipment with the most impactful automation opportunities within the food manufacturing industry—across the packaging, production, sanitation, product tracing, and quality control phases—enables companies to realize significant operational efficiencies and cost savings.
Read NowSunair Co. carries high-quality propane pumps and compressors from leading manufacturers such as Sundyne, Blackmer, and National Pump to ensure your operations perform safely and effectively.
Read Now2475 Wyandotte Road
Willow Grove, PA 19090
Phone: (215) 657-9800
Fax: (215) 657-9881
Email: sunairco@sunair.com
© Copyright 2025 Sunair Co.
Logos on this page are copyrights of their respective companies. The Sunair logo is a registered trademark of Sunair Co.
Leave a comment