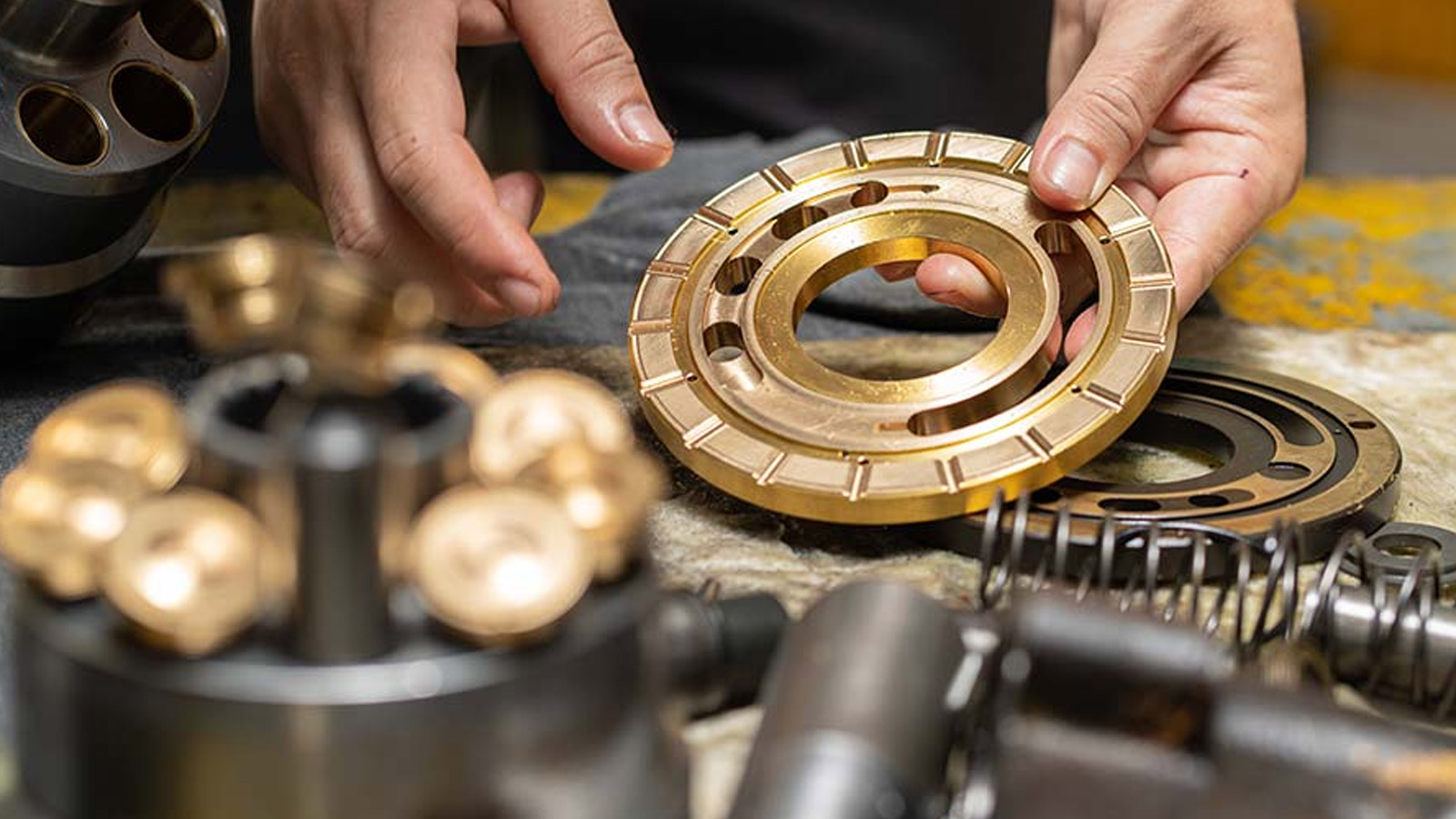
Published October 08, 2021 | 4 minute read
Published October 08, 2021 | 4 minute read
For nearly 50 years, Sunair Co. has been a premier provider of industrial pump equipment, products, repairs, and servicing throughout the northeastern United States.
“Sunair began as a small manufacturer’s representative organization and steadily grew over the years into a full-service stocking distributorship, with extensive service capabilities and complimentary product ranges,” explains Carl Ritger, Marketing Director at Sunair Co. “From a narrow focus, we’ve expanded into mechanical seals, lubricants and lubrication products, controls, and repair services.”
Founded in 1974 in Montgomery County, Pennsylvania, Sunair is dedicated to helping customers identify the right equipment for their applications, distributing high-quality industrial pumps, gas compressors and reliability products, and providing timely and effective repair and maintenance services.
“We are proud of our hands-on approach to diagnosing failure modes and consulting about pump system-related issues,'' continues Ritger. “[Our] wide range of products allow us to recommend a range of options for keeping equipment well-serviced or upgrading it to better-suited alternative technologies that improve reliability.”
With our robust inventory of Original Equipment Manufacturer spare and repair parts, Sunair Co. is the best option for industrial pump repair and servicing.
“We represent leading manufacturers of mechanical seals, lubricants, bearing isolators, desiccant breathers, et cetera, which when properly applied by our experts can vastly extend equipment life,” explains Ritger. “We service all types of pumps and seals, we also provide motor service. We also can consult about different pump technologies that could improve reliability of a pump service.”
Sunair is a Factory Authorized Service Center for all major product lines we distribute, and our expert team provides our customers with a wide selection of pumps and accessories, so we can help them choose the solution that suits them best. We also take a holistic approach to our installation and servicing, including pump system analysis, mechanical seal or sealless pump selection, troubleshooting, equipment lubrication analysis, and reliability training.
|
|
|
|
Our expert team will repair, upgrade, and install for our clients, 24 hours a day, 7 days a week, 365 days a year—from start-up and reliability upgrades to preventive maintenance and breakdown services.
Sunair’s team is comprised of an experienced staff of trained experts, including mechanical engineers, an industry veteran service manager, and factory trained and experienced service techs, with more than 125 years of combined industry experience.
“We are a company that has been in business for nearly 50 years and our team is composed of trained and highly experienced pump professionals,” says Ritger.
When clients choose Sunair for their pump equipment and repair services, they can expect “responsive and reliable service, a sense of urgency, expert advice, a hands-on approach, mechanical precision, insight into failure modes, and passion about recommending reliability upgrades,” he explains.
Our technicians are some of the most experienced pros in the region and we have two engineers on staff with PSAP (Pump Systems Assessment Professional) certifications. Using state-of-the-art systems analysis software, ultrasonic flow meter and other diagnostic tools, we can perform on-site flow measurement and systems analysis services to help you improve the energy efficiency and reliability of your pumping systems.
Regarding our pump repair services, we guarantee reliable, leak-tight performance and ship every repair with a 12-month warranty.
Sunair is the trusted service center for the mid-Atlantic region for everything from installation to repair and replacement—providing our customers with best-in-class solutions for their everyday applications.
From installation with value-added services to reliability upgrades, to regular maintenance and breakdown service, we do it all. And with our factory trained and experienced technicians, well- equipped facilities, fully warranted service, and innovative products and pump technologies, you can rest assured that when you work with Sunair Co. you’re working with the best experts and equipment in the industry.
Our experienced team of specialists provide expert repairs, upgrades, installations and professional maintenance services for centrifugal pumps, positive displacement pumps, vacuum pumps, and more to help keep your operations running smoothly.
Receive the latest industry news, once a month. Unsubscribe anytime.
To determine the size of a component mechanical seal, measure the inside diameter of the seal face, the length of the spring, and diameter and thickness of the stationary seat.
Read NowDesigned to handle various hydrocarbons in accordance with the high standards of the American Petroleum Institute, API pumps ranging from end suction to vertical turbine models are commonly used in the petroleum, petrochemical, and natural gas industries.
Read NowRegularly inspecting your mechanical seals and monitoring various factors that could contribute to failure or leakage will help extend their lifespan, while ensuring operational efficiency and safety.
Read NowPairing Sunair Co.’s high-quality equipment with the most impactful automation opportunities within the food manufacturing industry—across the packaging, production, sanitation, product tracing, and quality control phases—enables companies to realize significant operational efficiencies and cost savings.
Read NowSunair Co. carries high-quality propane pumps and compressors from leading manufacturers such as Sundyne, Blackmer, and National Pump to ensure your operations perform safely and effectively.
Read Now2475 Wyandotte Road
Willow Grove, PA 19090
Phone: (215) 657-9800
Fax: (215) 657-9881
Email: sunairco@sunair.com
© Copyright 2025 Sunair Co.
Logos on this page are copyrights of their respective companies. The Sunair logo is a registered trademark of Sunair Co.
Leave a comment