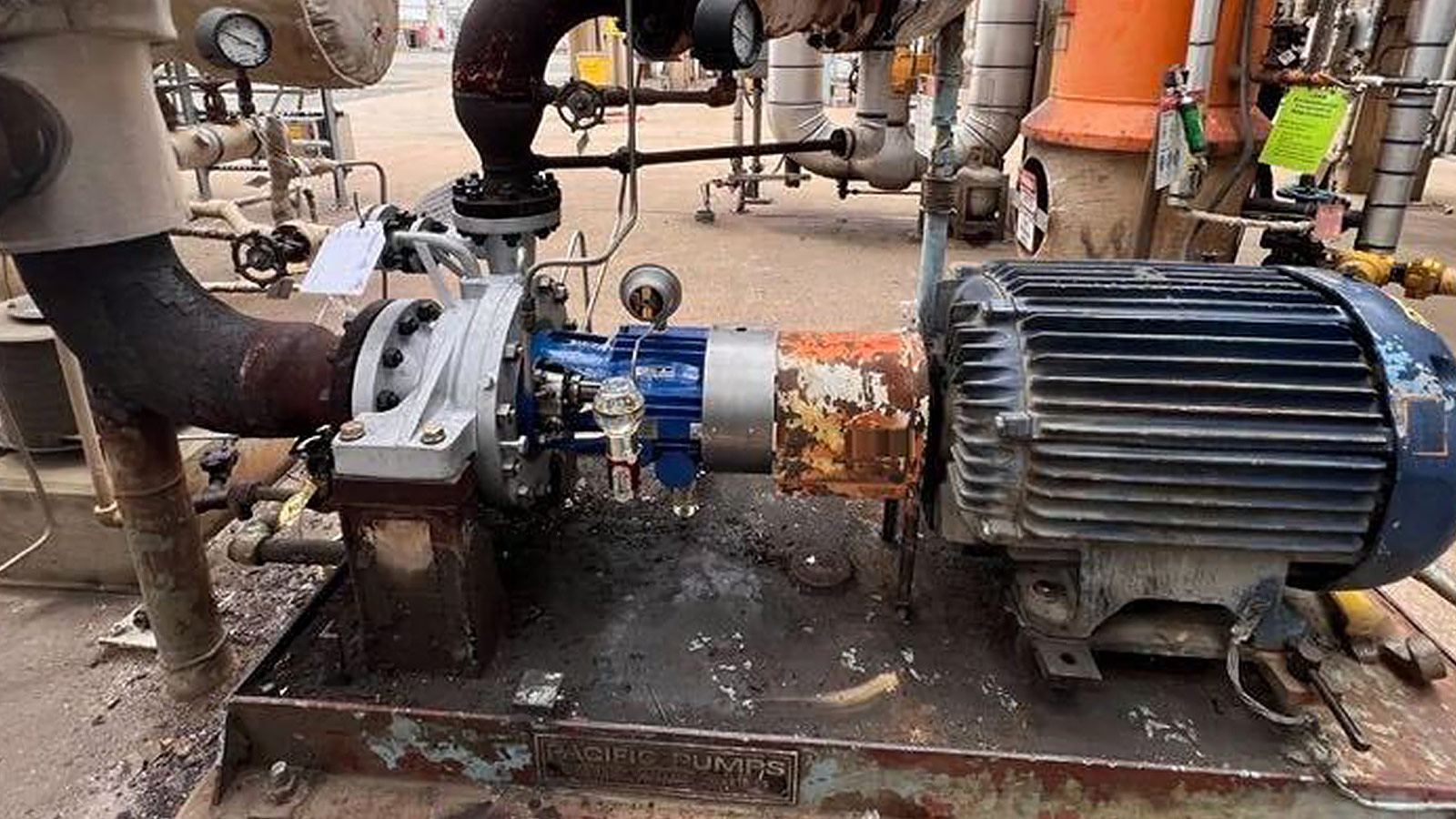
Published January 19, 2023 | 3 minute read
Published January 19, 2023 | 3 minute read
Sunair Co. works with the best pump and equipment reliability companies in the industry to provide a wide array of products, services, and top-of-the-line solutions to help maximize your operational performance and efficiency.
When the managers of an oil refinery in the Northeast sought to rerate and optimize one of its process units, they were limited by an existing, legacy pump with a much higher minimum continuous safe flow rate than required.
They turned to Sunair Co. and our partner Sundyne—a premier designer and manufacturer of industrial pumps and compressors for the process fluid and gas industries—for the best solution.
The refinery was having problems running their existing pump at the preferred flow rate, resulting in premature failures and reduced production efficiencies.
To make matters worse, the existing piping wasn't compatible with the recommended pump for the job—a low flow Sundyne SMKL horizontal overhung API 610 OH2 model. Having worked with Sundyne’s SMKL pumps before, the plant reliability engineers and operators knew it would provide the precise flow rate they were seeking to achieve, but required additional assistance to implement the new pieces of equipment.
Sundyne worked with the refinery to design and cast a custom volute so the pump could replace the old model, without requiring expensive piping modifications.
The plant was able to quickly install the pump, avoiding any unscheduled downtime or unexpected outages. The new, custom volute also averted a costly retrofit.
Within hours, the plant was back up and running, with process unit rates adjusted for optimal performance, and the pump operating at desired flow rates. The upgrade has resulted in improved pump reliability, higheruptime, and enhanced production.
The commissioning process went smoothly, and the unit’s spare is currently in production, to safeguard against future potential unplanned downtime. Sunair Co. and Sundyne are now looking forward to evaluating additional opportunities to upgrade, rerate, or retrofit other existing assets at the facility.
Sunair Co. is a full-service Sundyne industrial supplier and Authorized Service Center, providing a diverse line of pumps and equipment reliability products, as well as installation, repair, and maintenance services—ensuring your industrial operations run reliably and efficiently.
Have an upgrade or retrofit project? Give us a call to schedule a free, on-site pump survey and consultation.
Sunair can help with a variety of other Sundyne retrofit solutions, including but not limited to:
Sundyne SMKL and SMKLo API 610 OH2 horizontal end-suction pumps boast a rugged design capable of running continuously for years.
They’re specifically engineered to comply with the exacting API 610 standards for OH2 pumps. They are an efficient, reliable, and smart choice for use in oil and gas, petrochemical, power, and other demanding industries requiring heavy-duty, API-compliant equipment.
The SMKL line also uses Sundyne’s industry-leading, straight radial-vane Barske impeller and diffuser hydraulics, and is also a variation of the model SMK, with a closed Francis- vane impeller. SMKLo models incorporate Sundyne’s market-leading inducer technology for extreme low NPSHR applications.
Receive the latest industry news, once a month. Unsubscribe anytime.
To determine the size of a component mechanical seal, measure the inside diameter of the seal face, the length of the spring, and diameter and thickness of the stationary seat.
Read NowDesigned to handle various hydrocarbons in accordance with the high standards of the American Petroleum Institute, API pumps ranging from end suction to vertical turbine models are commonly used in the petroleum, petrochemical, and natural gas industries.
Read NowRegularly inspecting your mechanical seals and monitoring various factors that could contribute to failure or leakage will help extend their lifespan, while ensuring operational efficiency and safety.
Read NowPairing Sunair Co.’s high-quality equipment with the most impactful automation opportunities within the food manufacturing industry—across the packaging, production, sanitation, product tracing, and quality control phases—enables companies to realize significant operational efficiencies and cost savings.
Read NowSunair Co. carries high-quality propane pumps and compressors from leading manufacturers such as Sundyne, Blackmer, and National Pump to ensure your operations perform safely and effectively.
Read Now2475 Wyandotte Road
Willow Grove, PA 19090
Phone: (215) 657-9800
Fax: (215) 657-9881
Email: sunairco@sunair.com
© Copyright 2025 Sunair Co.
Logos on this page are copyrights of their respective companies. The Sunair logo is a registered trademark of Sunair Co.
Leave a comment