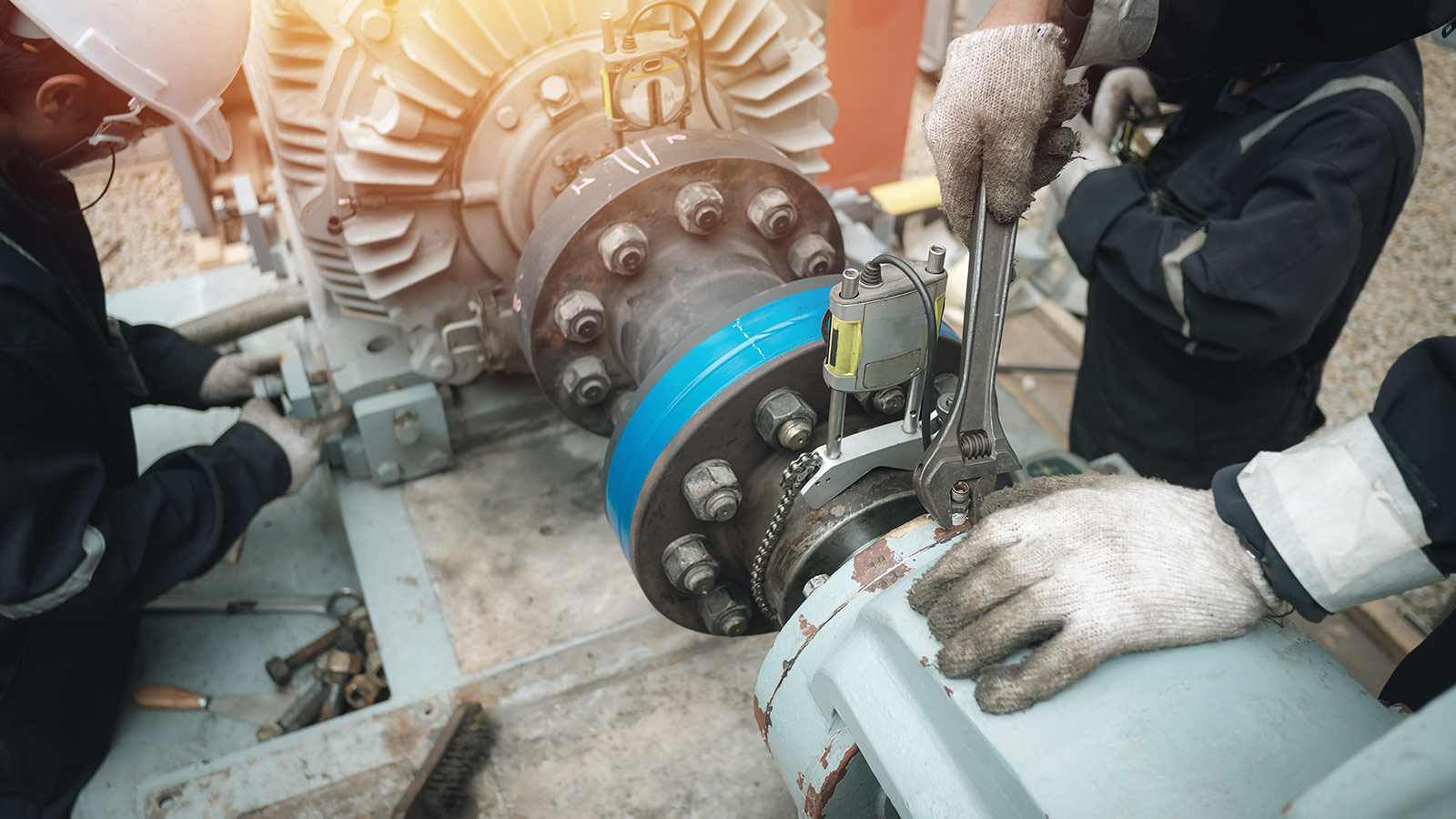
Published May 05, 2021 | 3 minute read
Published May 05, 2021 | 3 minute read
Progressive cavity pumps are also commonly referred to as progressing cavity pumps, ProCav pumps, PC pumps, PCPs, or single screw pumps. These versatile pumps have a wide variety of applications across multiple industries.
Here is the Sunair Co. definitive guide to progressive cavity pumps.
Progressive cavity pumps (PCPs) are positive displacement pumps, which simply means they work by repeatedly enclosing a fixed volume of fluid and moving it through the system. What makes PCPs unique is how they create these enclosures.
The pumping element is a single, helical-shaped screw-like rotor (hence the term screw pump) that rotates inside of an elastopolymer or rubber stator. These form a series of pockets which push liquid through the pump in a spiral, pocket by pocket, as the rotor turns. This allows PCPs to provide a constant, pulsation-free flow that is directly proportional to pump rotational speed.
There are numerous advantages to using progressive cavity pumps, depending on what kind of liquid transfer you’re performing, the required flow rate and pressure, or even the properties of the fluid you’re working with, such as viscosity, abrasiveness, temperature, solids content, and shear-sensitivity.
One important use for PCPs is to efficiently pump high-viscosity fluids without significantly increasing power consumption. Other positive displacement pumps and centrifugal pumps either have to greatly increase power consumption—and, by extension, the cost of transfer—or simply cannot move high-viscosity fluids without a marked drop in efficiency and increased lifecycle cost associated with the pump. The unique helical rotor and double helical pockets created by the rotor and stator enable PCPs to move both Newtonian and non-Newtonian liquids, such as paint, oil, sludge, and slurry.
Progressing cavity pumps are further able to handle a wide range of liquids with or without solids that may be abrasive, toxic, shear-sensitive, thin, or highly viscous.
Finally, thanks to the design of the rotor and stator, PCPs have very little shearing force or pulsation, resulting in gentle, continuous fluid transport, no matter the speed at which you set the rotor.
What are the disadvantages of progressive cavity pumps?
PCPs are not self-lubricating. Like many other pump types: if they run dry, they will fail, and require costly repairs. That said, an optional temperature sensor or motor load monitor will protect pumps from mis-operation.
Until recently, most PCPs were not adjustable for changes to their internal clearances due to wear. At least one PCP manufacturer offers the ability for the user to externally adjust the stator-to-rotor clearance and to reduce maintenance costs and total cost of ownership with a unique maintain-in-place design.
PCPs boast many applications across many industries. Here are several of the most common in the tri-state region:
Oil & Gas
PCPs are a great option for petroleum products transfer and are available in API-compliant configurations. They are also well suited for use in API separator services because their suction lift capabilities and low shear performance characteristics help prevent emulsification.
Paper Production
The helical nature of the PCP rotor makes this pump particularly suitable for slurry. In fact, PCP systems can optimize paper production processes in all steps of the process, including the pulper, paper machine, coating, and waste treatment. If you use a variable frequency drive, for example, a PCP can pump diluted slurry at variable but precise rates and even add necessary additives, such as bleaching chemicals, fixing agents, and other caustics that would cause fast wear and tear to other pumps.
Wastewater Treatment
Wastewater creates a high-viscosity sludge that often includes solids and easily clogs other kinds of pumps. The ability to handle abrasives, solids, and fluids of varying sizes and viscosities, as well as the heavy-duty nature of a PCP, makes it perfect for handling sludge treatment. PCPs can also be used in macerating and thickening processes.
General
PCPs are also great for metering and dosing across industries, as well as pumping any shear-thinning liquids that need low-shear transfer and any processing that might include solids, abrasives, or caustic liquids. They are often used in cosmetics production, fruit and vegetable processing, and recycling numerous common materials. Sanitary versions are available for transfer and no-pulsation metering of shear sensitive pharmaceutical products and even food products like whole chicken breasts.
Sunair is the tri-state leader for pumps and custom pump systems. Our team of experts can help you design a progressive cavity pump system customized to your application and needs. Contact us today.
Receive the latest industry news, once a month. Unsubscribe anytime.
To determine the size of a component mechanical seal, measure the inside diameter of the seal face, the length of the spring, and diameter and thickness of the stationary seat.
Read NowDesigned to handle various hydrocarbons in accordance with the high standards of the American Petroleum Institute, API pumps ranging from end suction to vertical turbine models are commonly used in the petroleum, petrochemical, and natural gas industries.
Read NowRegularly inspecting your mechanical seals and monitoring various factors that could contribute to failure or leakage will help extend their lifespan, while ensuring operational efficiency and safety.
Read NowPairing Sunair Co.’s high-quality equipment with the most impactful automation opportunities within the food manufacturing industry—across the packaging, production, sanitation, product tracing, and quality control phases—enables companies to realize significant operational efficiencies and cost savings.
Read NowSunair Co. carries high-quality propane pumps and compressors from leading manufacturers such as Sundyne, Blackmer, and National Pump to ensure your operations perform safely and effectively.
Read Now2475 Wyandotte Road
Willow Grove, PA 19090
Phone: (215) 657-9800
Fax: (215) 657-9881
Email: sunairco@sunair.com
© Copyright 2025 Sunair Co.
Logos on this page are copyrights of their respective companies. The Sunair logo is a registered trademark of Sunair Co.
Leave a comment