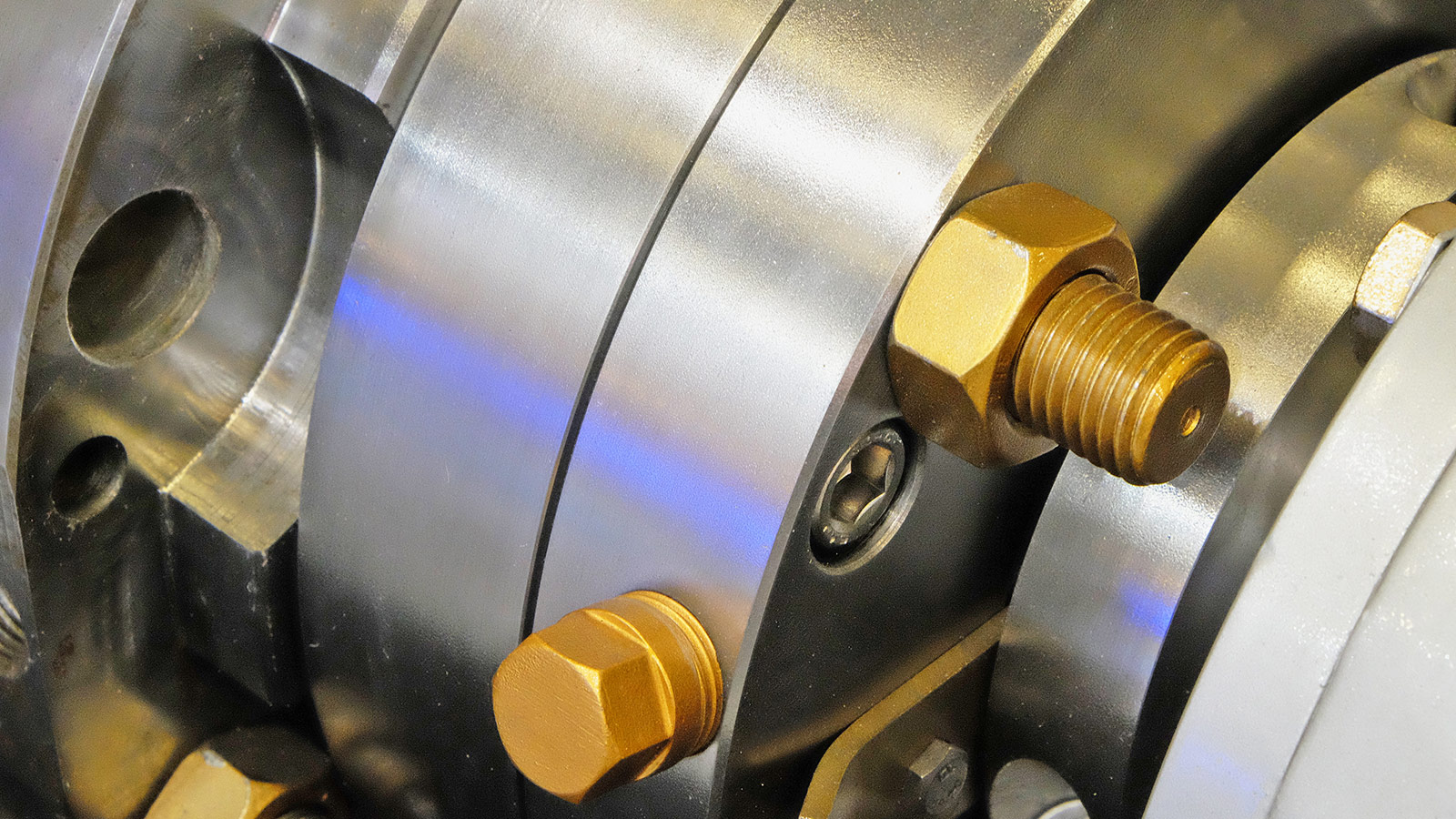
Published June 02, 2021 | 2 minute read
Published June 02, 2021 | 2 minute read
When developing a system for processing and transferring liquids, gases, and slurries, the pumps and compressors you choose are central to ensuring reliability and maximum efficiency, no matter your industry or application. They’re not the only components that matter, however.
Mechanical seals are the unsung heroes of industrial processing. They may be small, but they are absolutely critical to ensuring environmental safety and process integrity. Choosing the wrong seals, however, can lead to expensive equipment failures and downtime, so choosing the right model for your intended application is essential.
Here’s everything you need to know about mechanical seals.
Simply put, a mechanical seal is a device used to contain pressurized fluid or gas to prevent leaks. You’ll most often find mechanical seals on rotating equipment such as pumps, compressors, mixers, steam turbines, and blowers.
Without a proper seal in place, the high pressures used to transport liquid or gas within a pump or compressor will force that same liquid or gas out into the external – or lower pressure – environment, resulting in leaks, waste, and environmental concerns.
Mechanical seals are important for two main reasons:
Furthermore, while pump packing is a popular method of preventing leakage, it’s not nearly as efficient as using a mechanical seal, as this practice increases operating horsepower and damages the equipment shaft.
Mechanical seals have three core components: the stationary and rotating faces that comprise the primary seal, plus the static elements like elastomers and gaskets. The stationary part fits into the pump housing and are sealed with a static gasket or O-ring. Meanwhile, the rotating portion locks onto the pump, mixer, or compressor shaft and rotates with a very thin gap between it and the stationary face, which creates a tight orifice that reduces the higher sealing chamber pressure down to atmospheric pressure.
Mechanical seals work in one of two ways: either a rotating shaft moves through the stationary housing, or the housing rotates around the shaft. This configuration largely depends on application and sealing needs, though rotating shafts are much more common.
Depending on what kind of seal you use, either the stationary or the rotary components will be installed with spring loading to accommodate any shaft movements and manufacturing tolerated misalignments – i.e., misalignments that are within acceptable use parameters and do not require correction.
When designing your system, you should keep in mind that all mechanical seals require lubrication between the seal faces to reduce friction and prevent damage, or even breakage, as the two faces slide past each other.
There are so many different kinds of mechanical seals on the market right now, all with different installation and maintenance needs, that determining the optimal one may seem overwhelming.
Your best bet is to consult with an experienced company staffed with a knowledgeable team of highly trained experts, such as Sunair.
Sunair Co. has provided customers with high-quality commercial and industrial equipment, including mechanical seals, to organizations large and small, for all industries and applications, since 1974. We hand-pick our sales team for their expertise and ability to design custom systems for our clients.
Receive the latest industry news, once a month. Unsubscribe anytime.
To determine the size of a component mechanical seal, measure the inside diameter of the seal face, the length of the spring, and diameter and thickness of the stationary seat.
Read NowDesigned to handle various hydrocarbons in accordance with the high standards of the American Petroleum Institute, API pumps ranging from end suction to vertical turbine models are commonly used in the petroleum, petrochemical, and natural gas industries.
Read NowRegularly inspecting your mechanical seals and monitoring various factors that could contribute to failure or leakage will help extend their lifespan, while ensuring operational efficiency and safety.
Read NowAir-operated double-diaphragm (AODD) pumps utilize compressed air and dual chambers to transport fluids safely and efficiently in support of a wide range of industrial applications.
Read NowSunair Co. carries high-quality propane pumps and compressors from leading manufacturers such as Sundyne, Blackmer, and National Pump to ensure your operations perform safely and effectively.
Read Now2475 Wyandotte Road
Willow Grove, PA 19090
Phone: (215) 657-9800
Fax: (215) 657-9881
Email: sunairco@sunair.com
© Copyright 2025 Sunair Co.
Logos on this page are copyrights of their respective companies. The Sunair logo is a registered trademark of Sunair Co.
Leave a comment